Banana chips have become a popular snack worldwide, prompting entrepreneurs to invest in banana chips manufacturing plants. The cost of establishing such a plant can vary significantly depending on several factors, with the degree of automation playing a pivotal role. In this article, we will delve into the intricacies of banana chips manufacturing plant costs, exploring the range from $20,000 to $150,000 based on automation levels.
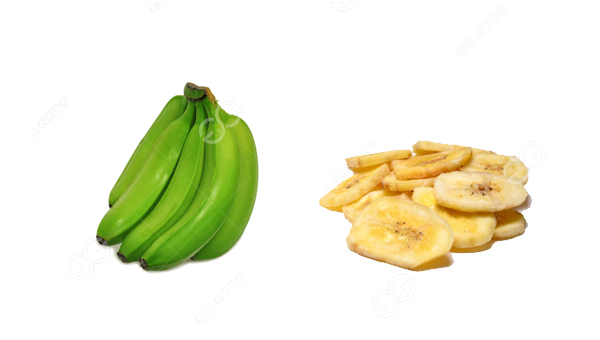
Factors influencing costs:
Scale of production: The scale of production is a crucial determinant of the overall cost. Larger plants with higher production capacities generally require more sophisticated equipment and infrastructure, contributing to increased initial investments.
Automation levels: The degree of automation has a direct impact on both the upfront and operational costs. A fully automated plant, equipped with cutting-edge machinery and robotics, will naturally incur higher costs compared to a semi-automated or manual operation.
Quality and features of machinery: The quality and features of the machinery used in the plant play a significant role in cost determination. High-quality, technologically advanced equipment may come at a premium but can enhance efficiency and product quality, potentially justifying the initial investment.
Raw material sourcing: The cost and availability of raw materials, specifically bananas, can vary depending on geographical location and seasonal factors. Establishing a reliable and cost-effective supply chain for bananas is essential for managing operational costs.
Location and infrastructure: The geographical location of the manufacturing plant can influence costs. Factors such as land prices, labor costs, and utility expenses can vary from one region to another, impacting the overall budget for establishing and running the plant.
Cost breakdown:
Land and infrastructure: The cost of acquiring land and developing the necessary infrastructure, including the construction of the manufacturing facility, storage, and utilities, constitutes a significant portion of the initial investment.
Machinery and equipment: This includes the cost of peeling machines, slicing equipment, frying apparatus, packaging machinery, and any additional technology adopted for automation. The level of sophistication in machinery directly correlates with the overall cost.
Labor: Labor costs encompass hiring and training staff for various roles in the manufacturing process. Highly automated plants may require fewer manual operators but may demand skilled technicians for maintenance and troubleshooting.
Raw materials: The cost of bananas, as well as other ingredients such as oil and seasoning, contributes to the overall production cost. Establishing contracts with reliable suppliers can help manage raw material expenses effectively.
Regulatory compliance and quality assurance: Adhering to regulatory standards and implementing quality assurance measures involves additional costs. This includes obtaining necessary certifications, implementing safety protocols, and investing in quality control processes.
The investment required to establish a banana chips manufacturing plant can vary widely based on factors such as automation levels, scale of production, and location. Entrepreneurs need to carefully assess their business goals, market demand, and budget constraints before making decisions about the degree of automation and the associated costs. While a fully automated plant may have a higher upfront cost, it can lead to long-term operational efficiency and product consistency, ultimately contributing to the success of the venture.